The Role of Quartz Powder in Modern Foundry Techniques
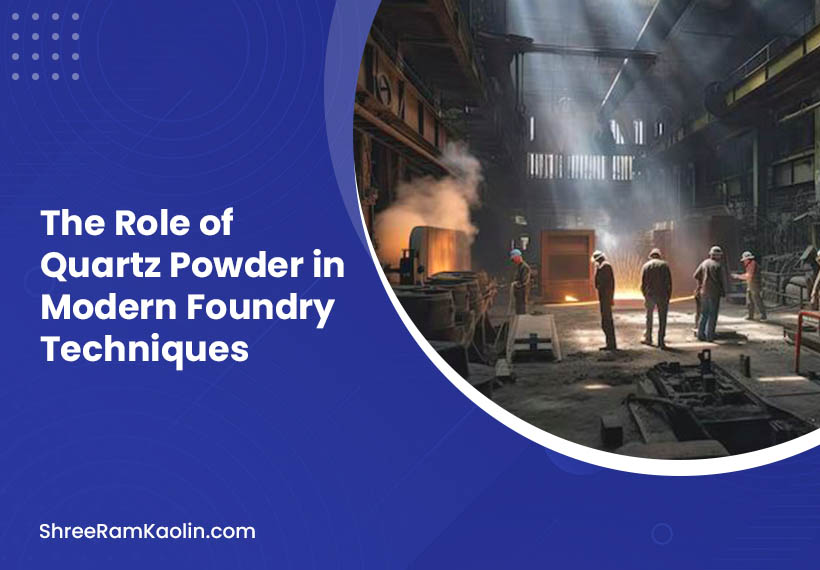
Foundries play an indispensable part in manufacturing industries worldwide, manufacturing metal components and parts through various casting processes. Casting involves melting metal into liquid form before pouring it into moulds for solidification into desired shapes – with mould materials having an enormous influence over the quality and performance of finished castings.
Quartz powder has become indispensable in modern foundry techniques, contributing significantly to improved casting quality, extended furnace lifespan and overall cost reductions.
What is Quartz Powder?
Quartz powder is a finely ground form of quartz, an inorganic mineral composed primarily of silicon dioxide (SiO2). It’s produced through mining and processing rocks rich with quartz crystals like sandstone or quartzite, which are then processed further to become powder.
Granular material then results from processing the quartz powder according to your application requirements, providing an adjustable particle size range depending on application needs.
Properties of Quartz Powder
Quartz powder possesses several unique properties that make it well-suited for foundry applications:
- Chemical Inertness: Quartz powder is highly resistant to chemical attacks and does not react with molten metals or other materials used in foundries, ensuring consistent performance.
- High Melting Point: With a melting point of around 1,700°C (3,092°F), quartz powder can withstand the extreme temperatures encountered in foundry operations without undergoing significant degradation or phase changes.
- Thermal Stability: Quartz powder exhibits excellent thermal stability, maintaining its physical and chemical properties even at elevated temperatures, making it suitable for high-temperature applications.
- Other Key Properties: Quartz powder is also known for its high compressive strength, low thermal expansion, and good insulating properties, further enhancing its suitability for foundry use.
Applications of Quartz Powder in Foundries
As a Parting Material
Quartz powder has multiple applications within foundries, one being as parting material. Parting materials serve to separate molten metal from mould surfaces to avoid metal-mould interactions while simultaneously providing for a seamless release upon solidification of castings.
Foundries can improve casting surface finishes and decrease defects such as metal penetration or sticking by directly applying a thin coat of quartz powder onto their mould surfaces. With its chemical inertness and high-temperature stability, quartz powder makes an excellent material choice for this use case.
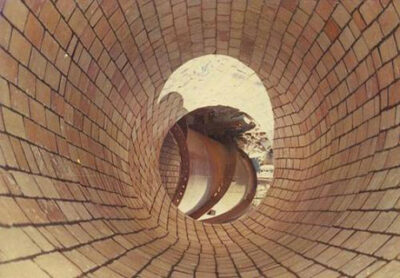
Quartz powder plays a central role in manufacturing refractory linings used to line furnaces and high-temperature equipment in foundries.
Refractory mixes made of clays, ceramics, and quartz powder can create durable linings capable of withstand harsh environments in furnaces.
Quartz powder adds thermal shock resistance, increasing the service life of furnace linings, which not only increases overall foundry efficiency but also decreases costs through less frequent replacement needs and cost-cutting opportunities.
In Sand Casting
Quartz powder plays an essential part in the sand casting process used by foundries worldwide, including creating moulds using sand, binder and additives such as quartz powder to form moulds for casting processes such as sand casting.
In this technique, moulds are formed using a mixture of sand, binder and additives like quartz powder as preparation steps.
Quartz powder adds efficiency and economy to green sand (clay-bonded) or resin-bonded mould formulations by improving their shake-out properties, making the removal of castings from moulds after solidification simpler and stronger than before.
Furthermore, using quartz powder increases strength and reusability, leading to more cost-efficient casting operations.
Benefits of Using Quartz Powder
The use of quartz powder in modern foundry techniques offers numerous benefits, including:
Improved Casting Quality
Quartz powder provides excellent parting material properties while improving mold properties to minimize defects such as metal penetration, inclusions and surface irregularities in castings. This leads to improved dimension accuracy and higher-quality final products with reduced need for rework or rejections.
Increased Furnace Life
Quartz powder in refractory linings significantly extends the service life of furnaces and other high-temperature equipment used in foundries, thanks to its thermal stability and erosion resistance- qualities that help preserve linings’ integrity while decreasing replacement needs and associated downtime costs.
Cost Savings
Quartz powder’s benefits in foundries ultimately translate to cost savings for operations. By eliminating defects and improving casting quality while lengthening furnace lining lifespan, foundries can significantly decrease their costs associated with rework, rejections and maintenance – leading to greater operational efficiency and profit potential.
Proper Selection and Application
Importance of Particle Size
The particle size of quartz powder plays a pivotal role in its performance and behaviour in various foundry applications, with smaller particle sizes generally providing better surface coverage and parting properties, while larger particle sizes might be preferred for certain refractory mixes or casting applications.
Foundries must select an ideal particle size range to maximize performance and reap its advantages when working with quartz powder.
Customizing its distribution may improve desired properties while assuring consistent quality for castings produced.
Quality Control
Implementing stringent quality control measures is vital to ensure consistent performance and reliability from quartz powder used in foundry operations, including monitoring chemical composition, particle size distribution and levels of contaminants provided by suppliers.
Foundries can ensure their quartz powder meets required specifications by adhering to stringent quality standards and conducting regular tests and inspections, thus lowering risk from defects or operational issues and keeping their processes operating efficiently.
Environmental Considerations
quartz powder offers many advantages to foundry operations; however, its use should also be met with consideration of any environmental and health hazards it might present. Respirable crystalline silica found in quartz powder poses potential respiratory hazards if certain precautions are not observed.
Foundries must implement suitable safety measures, such as adequate ventilation systems, personal protective equipment (PPE) and employee training programs to combat quartz powder handling and exposure risks. Adherence to relevant environmental regulations and best practices is imperative in creating an ideal and safe work environment for their workforce.
Conclusion
Quartz powder has become indispensable in modern foundry techniques, helping improve casting quality while increasing furnace life and driving cost savings. Due to its chemical inertness, high melting point, and thermal stability properties, quartz powder is an excellent addition for use as parting materials, refractory lining materials, or casting processes such as sand casting.
As foundries embrace new technologies and optimize their use of quartz powder, its role will only become more vital. By employing effective quality control measures and harnessing its full potential for consistent performance and enhanced efficiency amidst today’s ever-evolving manufacturing landscape, foundries can harness quartz’s fullest potential and maintain an edge in this dynamic manufacturing sphere.